30/10/12
Muebles pochoclo.
Interieur: Belgian designer Carl de Smet of Noumenon has developed high-tech foam furniture that can be squashed to 5% of its original size for easy transportation and then expanded “like popcorn” by heating it up (+ movie + interview).
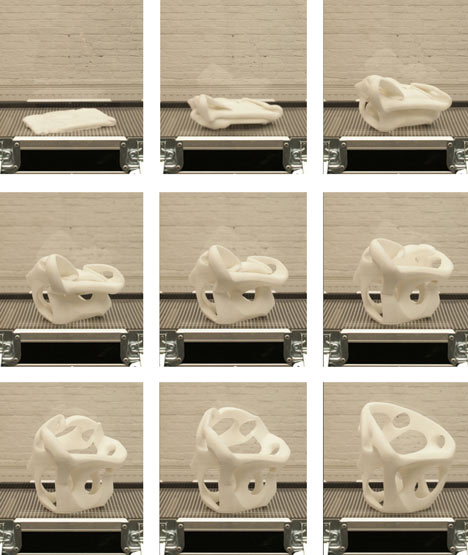
Under the proposal, which is still at the research stage, products made of polyurethane shape-memory polymers (SMPs) are compressed into flat, lightweight slabs (top left in the above sequence), meaning they take up very little space until they are required. When heated, the furniture returns to its original shape thanks to the “memory foam” properties of the material (see movie below).
“It’s light, so for shipping it’s almost taking up no space,” de Smet told Dezeen. “If it gets damaged and it’s heated again, [the damage] disappears. If you ship the packaging and something happens to it, it doesn’t matter because it isn’t the end product; that’s in the imprinted memory.”
The project evolved out of a research project to design a parabolic antenna for outer space that would be compressed to make a smaller payload on a spaceship, then expanded to full size when exposed to the sun’s rays. This project involved shape-memory alloys (SMAs) – advanced metals that perform in the same way as SMPs, but which are highly expensive.
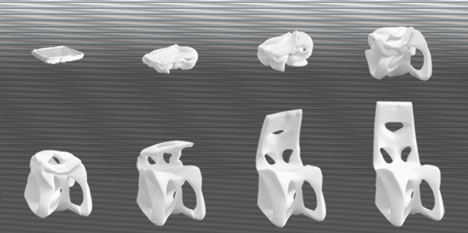
“I wanted to bring it back to daily life and not only use it for high technology projects, and for that the metals were too expensive,” says de Smet. “With polymers, when you produce them in large quantities, it’s affordable.”
At the moment the items need to be placed in a large heated environment like a sauna to reach the required temperature of 70 degrees, but de Smet is researching other ways of triggering the transition from the compressed to the expanded form, for example by “programming” the material to return to its remembered form when electricity is passed through it.
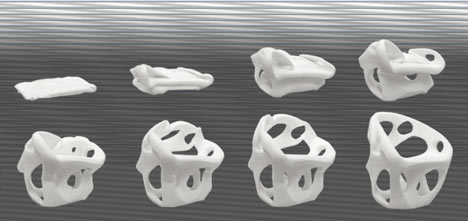
“[At the moment] it’s programmed [to expand] at 70 degrees, because of the logistics of transport,” de Smet said. “For example in the summer and the truck is stuck in traffic, then inside it is building up to 50 degrees and we don’t want the furniture to pop, like popcorn.”
The foam, which is strong enough to be structural, can be turned into furniture by milling solid blocks of the material or by injection moulding.
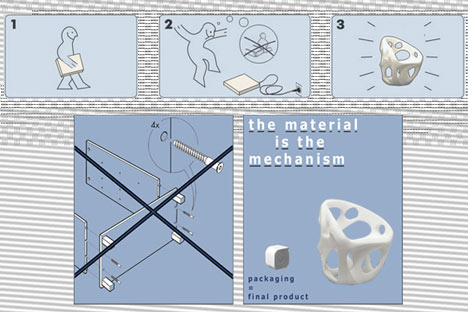
De Smet is exhibiting the project, including scale models of a foam armchair, at the Buda Factory building in Kortrijk, Belgium, as part of the Interieur 2012design biennale. The exhibition continues until 28 October. See all our stories about Interieur 2012.
Below is the interview with de Smet, conducted by Dezeen editor-in-chief Marcus Fairs:
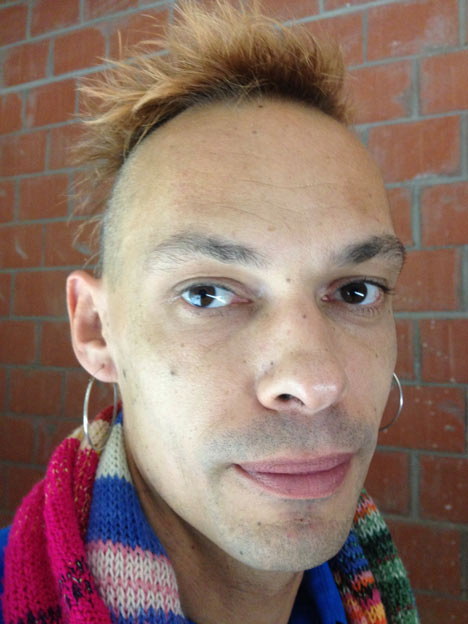
Marcus Fairs: Tell us about the Noumenon project.
Carl de Smet (above): It’s a research project that started five, six years ago, around the world of smart materials, smart polymers, which have the possibility to change shape. It means you can fix a temporary shape and then if you reach a certain temperature it can transform into an end product.
Marcus Fairs: What kind of material is it? It looks like a kind of foam.
Carl de Smet: It’s a kind of memory foam. Foam can have different densities; normal foam is really soft, spongy. But this one is rigid, so it’s strong, which means you can us it as a structural support. And when it becomes hot and when it wants to change form, it becomes soft.
Marcus Fairs: Is this a material you invented yourself or one that you discovered and found a use for?
Carl de Smet: These polymers have been around for 20 years but finally we are updating the material for design applications on a bigger scale.
Marcus Fairs: Was this something you discovered by mistake?
Carl de Smet: We didn’t discover it by mistake. In 2002/2003 I was doing a research project with shape-memory alloys; metals that are really well known. It was an idea to design a parabolic antenna for outer space. The idea was to bring a squeezed form out into space, connected to a spaceship. You unload it in the cold air then when you turn it to the sun the heat would open it and form an antenna. I really liked the idea of designing certain kinds of objects that have a performative behaviour. I wanted to bring it back to daily life and not only use it for high technology projects, and for that the metals were too expensive. As you know with polymers, when you produce them in large quantities, it’s affordable. That’s the reason I researched into plastics.
Marcus Fairs: So tell us how this could be used to create a product. Here you’ve got a model of an armchair.
Carl de Smet: It’s an armchair but the basic idea is that [you buy it] in a packaging shape. You buy a package, you come home to the story that everybody knows now: the special key from Ikea; you put everything together; you assemble it yourself. Here the material is making this move. The material is doing the work. Because the form in imprinted in the memory effect of the material.
Marcus Fairs: So you manufacture this chair and you compress it, you squash it?
Carl de Smet: Yes.
Marcus Fairs: How much smaller can you make it than the original?
Carl de Smet: We can reduce it to 20 times smaller. If you think about the form it’s a cellular structure, and inside the structure there is air and you can collapse this structure. Then it becomes like a slab.
Marcus Fairs: What’s the benefit of this? I imagine you can ship it much more efficiently.
Carl de Smet: It’s light, so for shipping it’s almost taking up no space. If it gets damaged and it’s heated again [the damage] disappears. If you ship the packaging and something happens it doesn’t matter because it isn’t the end product; that’s in the imprinted memory.
Marcus Fairs: How do you then turn the squashed product into the full-sized product?
Carl de Smet: For the moment it’s heat, but we are researching applications that will allow it to happen in households, because not everyone has a sauna at home where you can put furniture.
Marcus Fairs: So you have to put it in a very hot room?
Carl de Smet: At the moment it’s programmed to [expand at] 70 degrees, because of the logistics of transport. For example in the summer if there is a traffic jam and the truck is stuck in traffic, then inside it is building up to 50 degrees and we don’t want the furniture to pop, like popcorn. That’s the reason we calculated 70 degrees. It sounds quite high but when you think about logistics, that’s the minimum.
Marcus Fairs: How would you shape the product? With a mill?
Carl de Smet: It’s made with a mill but we can also do injection moulding. This is a kind of a polyurethane, or PU. In the car industry the fake leather is made out of PU. So we can do it like fake leather or fake wood; it’s just the finishing of the moulding process. It depends on the moulding and how you present it.
Marcus Fairs: What’s the scientific process that allows it to retain its memory?
Carl de Smet: If you look under a microscope at polymers you see a kind of spaghetti form. In this form you make chemical cross-links and that fixes the form and the trigger. Every time you compress or stretch it it remembers the connection points and cross links.
florero de resina facetado.
In the first of a series of movies about objects we curated for the Stepney Green Design Collection, east London designer Phil Cuttance describes the messy process of casting an extra-large version of his Faceture vase.
28/10/12
Shinya kimura.
Algo mas de esto...
metal.,
moto,
motos,
trabajo manual
25/10/12
Letreros.
Sign Cast from Edward Styles on Vimeo.
Algo mas de esto...
fundición,
metal,
trabajo manual
metalero
Algo mas de esto...
metal,
trabajo manual
Hay lago mas lindo que ver trabajar esta máquina.
Algo mas de esto...
cnc,
metal,
procesos productivos
Aserrín inflado.
well proven chair from Marjan on Vimeo.
Algo mas de esto...
aserrín,
locos.,
proceso creativo,
resinas
Armas de canción masiva.

a stringed instrument made from firearms
image © designboom
since 2008, mexican artist pedro reyes has been turning to weapons as a medium to address the crime rates in his native country
by transforming them into objects of social engagement. he first began working with palas por pistolas, a campaign which invited
citizens of the western mexican city of culiacán - a city known for high rates of gun-related deaths - to voluntarily donate illegal weapons.
rewards in the form of coupons redeemable at local stores for domestic appliances and electronics, where given to those who did.
the 1527 collected firearms were then crushed by steamroller, melted in a foundry and given to a major hardware store to be cast into
shovels which were then distributed to a number of institutions for adults and children to participate in the action of planing 1527 trees.
his most recent project 'imagine' is a set of 50 musical instruments also fabricated out of a variety of firearms including revolvers,
shot-guns, machine guns etc. commissioned by alumnos 47. the undertaking developed from a simple phone call that reyes received from
he government who had learned about palas por pistolas and informed the artist that there would be a public destruction of weapons taking place
in ciudad juarez. they asked him if he wanted to keep the discarded metal which would otherwise be buried. armed with 6700 pieces,
over the course of two weeks, working together with six musicians, he transformed the confiscated guns into a fully functioning orchestra
which include a flute, guitar and drum kit.
the objects of musical destruction are on display as part of the 'adhocracy' exhibition, curated by joseph grima at the istanbul design biennial 2012.
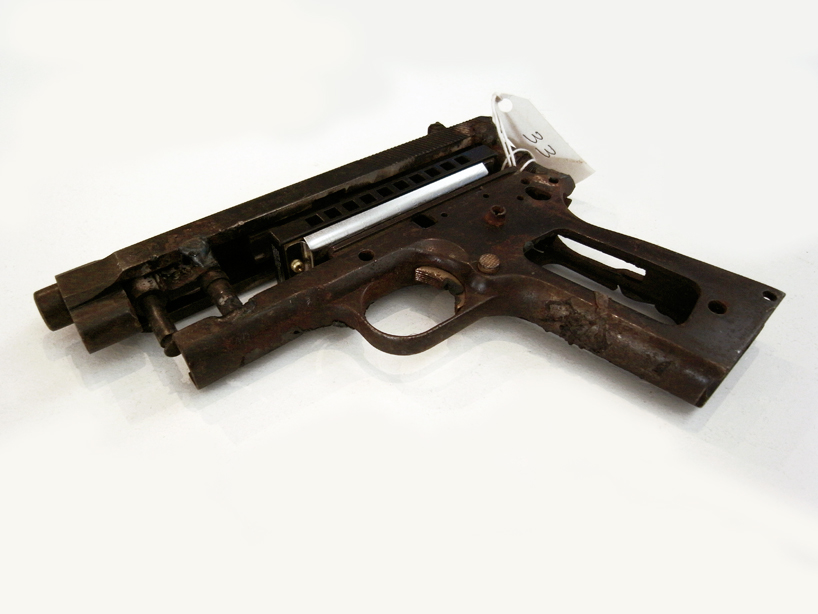
reyes' received more than 6000 weapons to create his orchestra
image © designboom

image © designboom
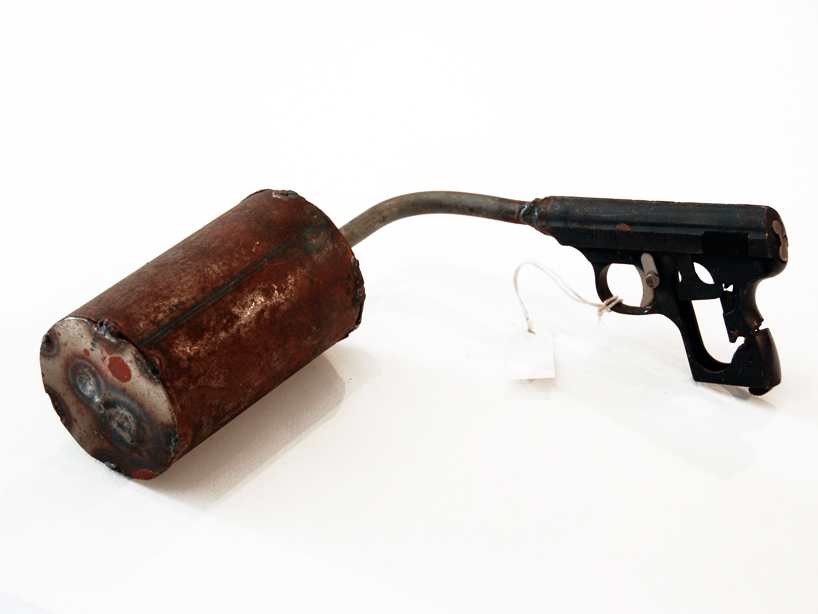
image © designboom
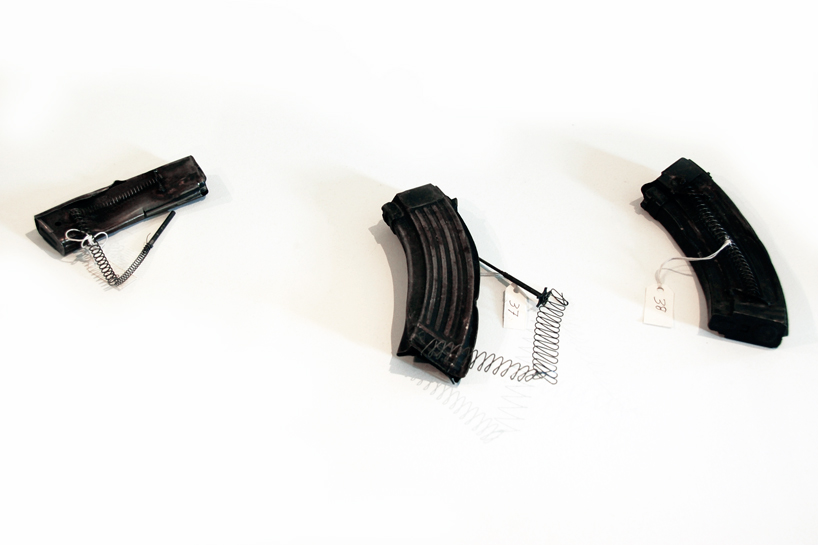
magazines from various firearms
image © designboom
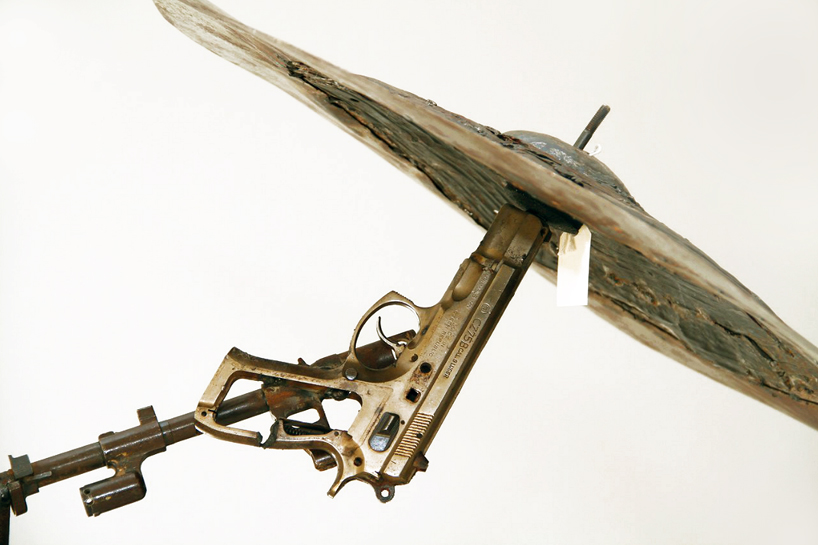
hat cymbal made from the discarded metal
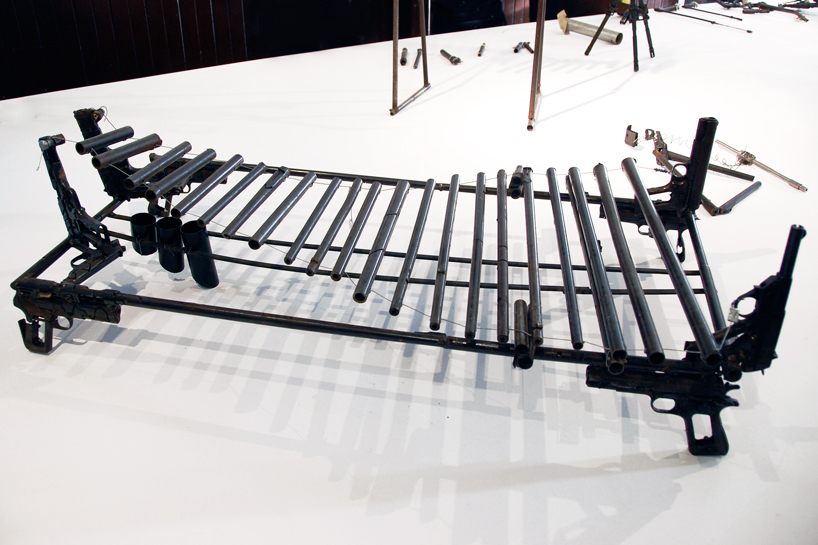
a xylophone made from barrels
image © designboom
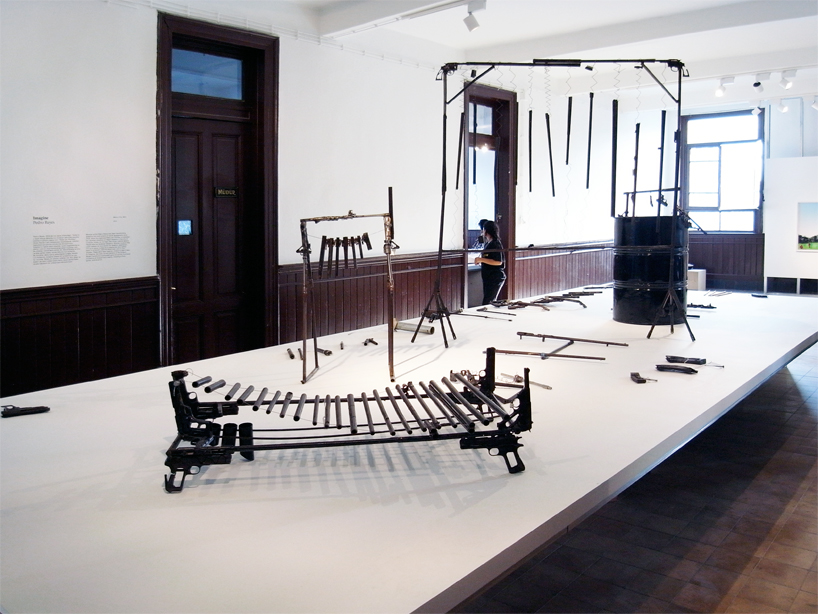
installation view of pedro reyes' instruments
image © designboom
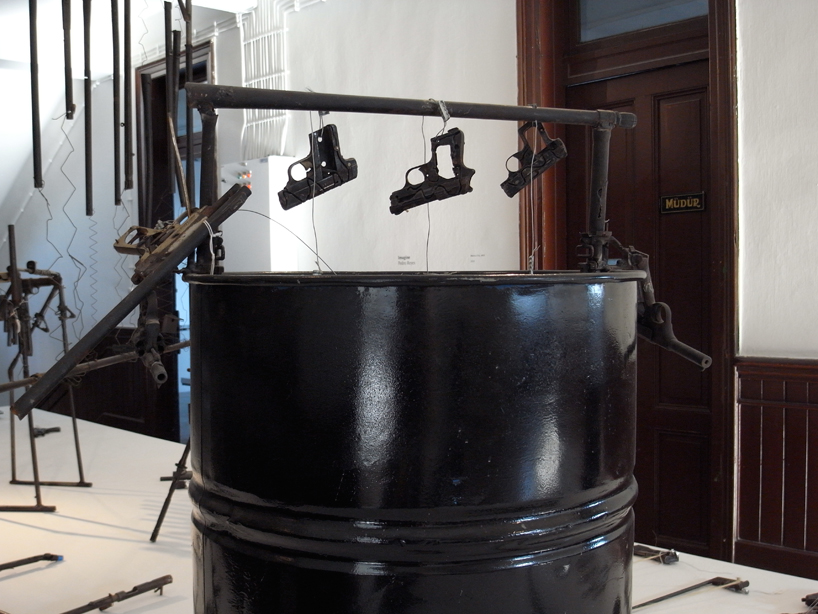
an interpreted version of the triangle
image © designboom
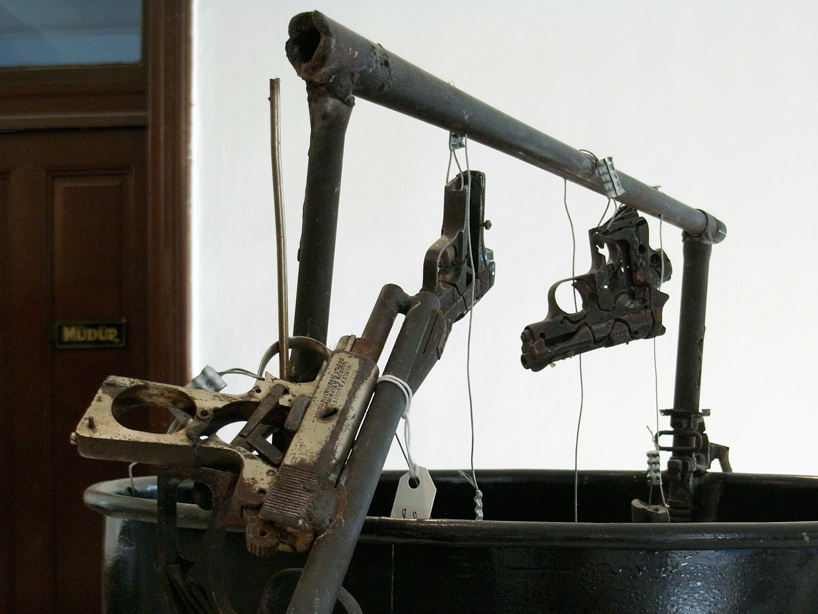
image © designboom
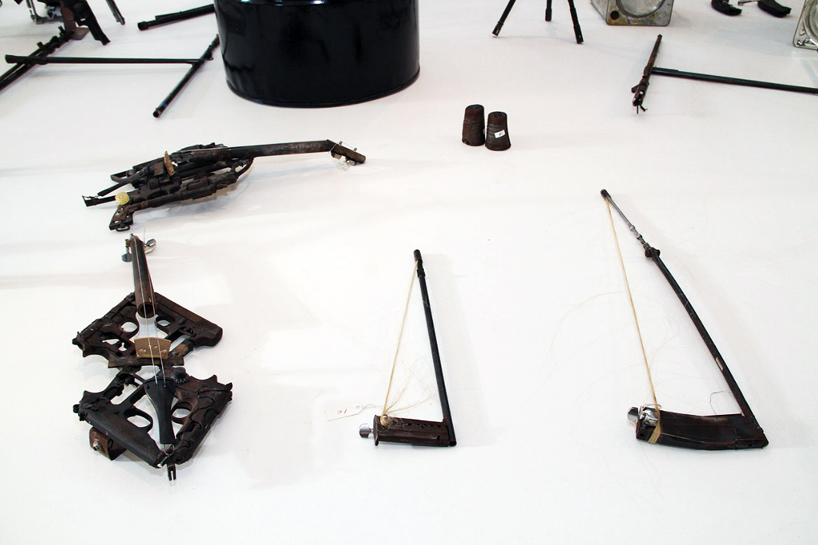
string instruments and bows
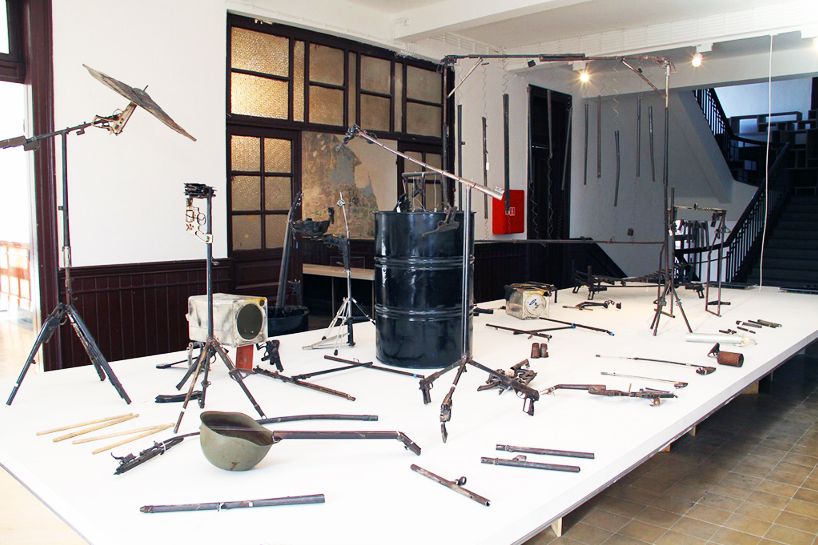
alternative exhibition view of the instruments which include cymbals, violins and guitar
a concert played using the musical instruments made from weapons
video courtesy of pedro reyes
the making of the instruments
video courtesy of pedro reyes
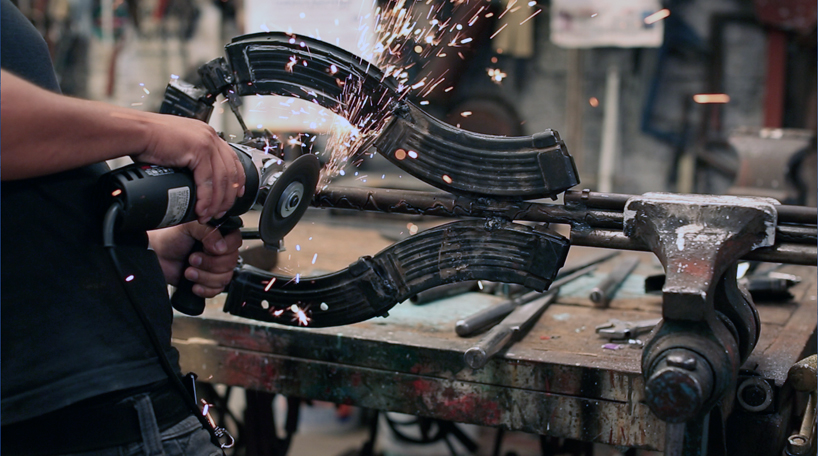
production of the instruments
photo by david franco for 192 courtesy of pedro reyes
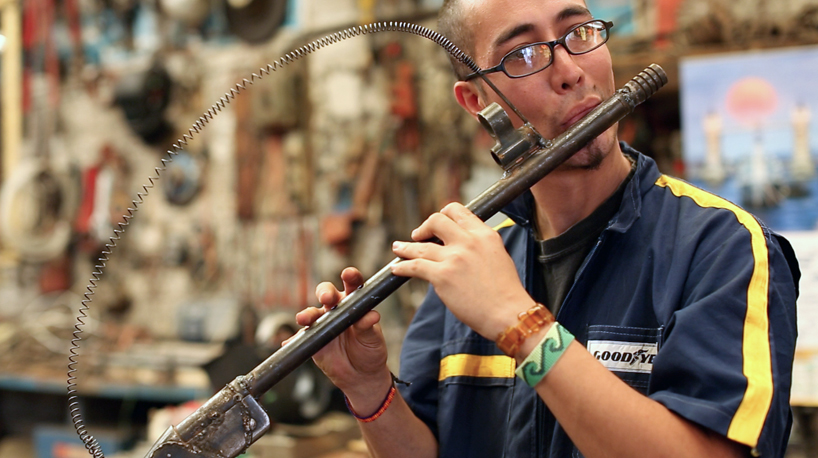
testing out the flute
photo by david franco for 192 courtesy of pedro reyes
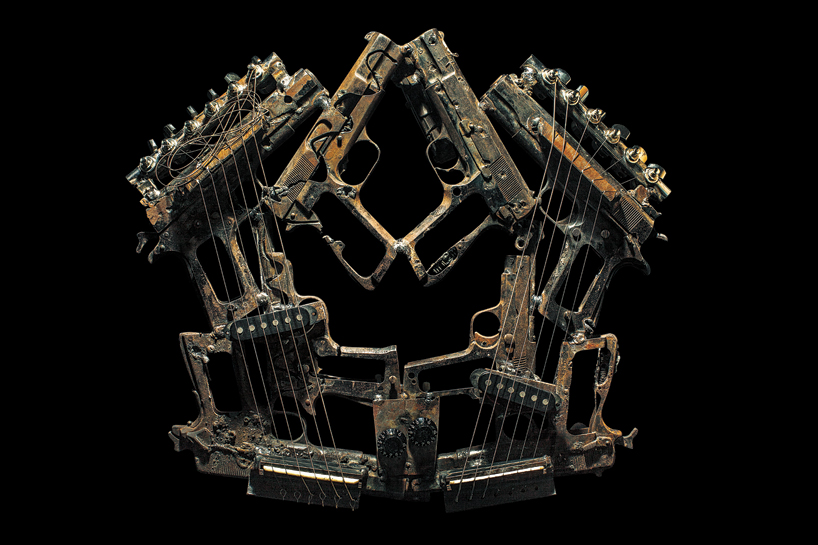
lyre
photo by david franco for 192 courtesy of pedro reyes
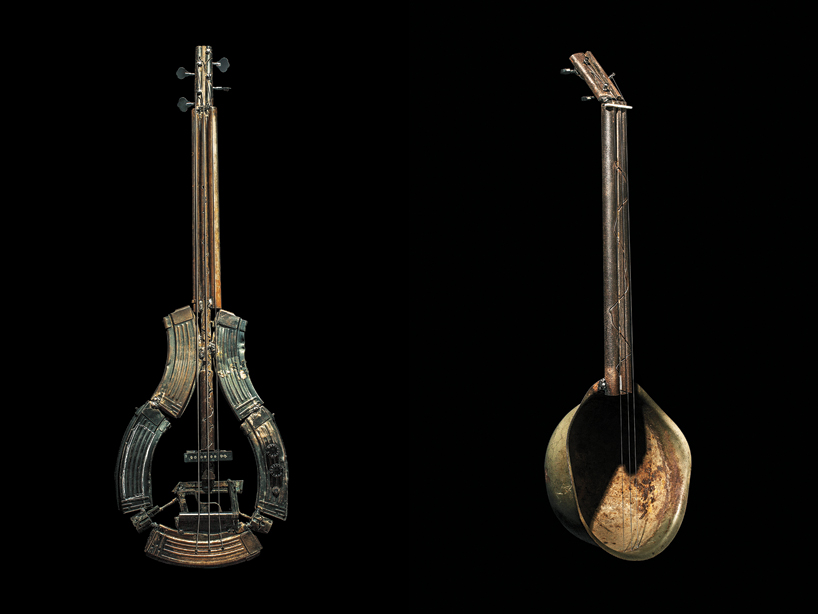
guitar and banjo
photo by david franco for 192 courtesy of pedro reyes
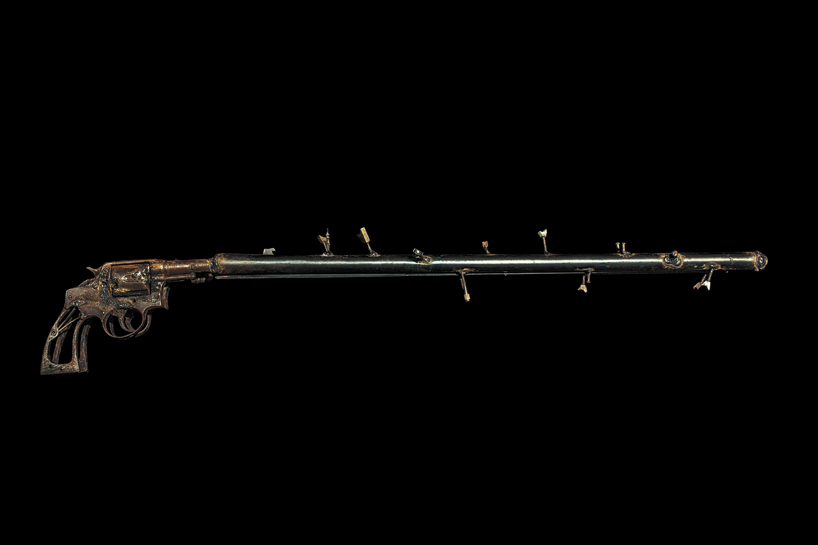
photo by david franco for 192 courtesy of pedro reyes
weapons undergoing mass destruction before being transformed into objects of social engagement
video courtesy of pedro reyes
Bachas, todo el proceso.
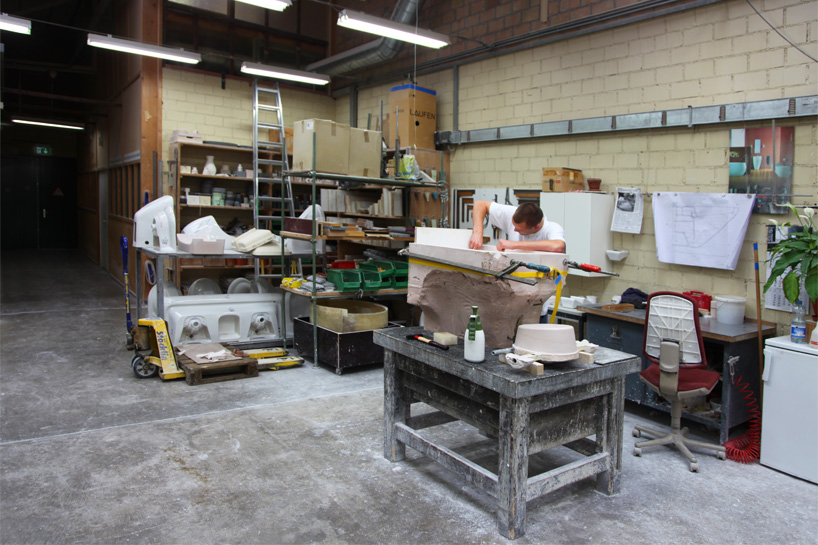
designboom visits LAUFEN's design development team, who work with new pieces from their first conceptualization through mold-making and prototype analysis as a design is prepared for production
above, jannik stöckli, an industrial ceramics apprentice, sands down a cast to meet technical specifications
image © designboom
designboom had a behind-the-scenes look at the LAUFEN ceramics factory, where we had a manufacturing tour of the
swiss company's fabrication process. we've documented the many steps and design considerations that go into the production
of bathroom fittings, offering a better understanding of the different design criteria and production methods required for these
everyday household pieces, as well as the way in which such an ancient material as ceramic is being utilized in high-tech
and industrial applications in the present day.
in this article, part of a longer behind-the-scenes series, let's get back to the very beginning of the life of a ceramic piece
by looking at the design development process. by far the most time-intensive stage of production, this process takes about
a year for each new design, from the first idea and briefing through when the piece is on the production lines. LAUFEN is
particularly esteemed in the design world for its collaborations with renowned industrial designers and architects towards
the creation of bathroom pieces. here the process can differ in its particularities: sometimes designers are approached to develop
new product lines, other times individuals submit ideas to LAUFEN in response to a product briefing, in which case the selection
of a designer and piece becomes part of the development process. anytime the company works with a new collaborator,
(s)he is invited to spend time in the factory learning a bit more about the methods and particularities of working with ceramic;
oftentimes these designers move on to engage in longer-term collaborations with the company.
marc viardot, director of marketing and products
looking more generally at the company's design philosophy, LAUFEN routinely conducts worldwide research surveys
to maintain a forward-looking perspective, asking architects, interior designers, and retailers to identify current trends
in bathroom culture, and report on the needs and desires expressed by consumers. while the research doesn't exclude
physical attributes such as colour or silhouette, LAUFEN is increasingly finding the focus on what marketing and products
director marc viardot terms 'wellness 2.0', the seamless integration of functionality and aesthetic as they affect an individual's
experience, within the greater context of a home.
ultimately, however, a successful concept depends on successful execution, and in order for any proposed piece to continue on in
the LAUFEN design process, it must pass a rigorous 'visibility analysis' in a team meeting of the plant manager and supervisors
in the casting, glazing, and firing departments. here, these professional craftsmen examine a design to ensure that it can be
produced within the constraints that the ceramic material and production process defines.
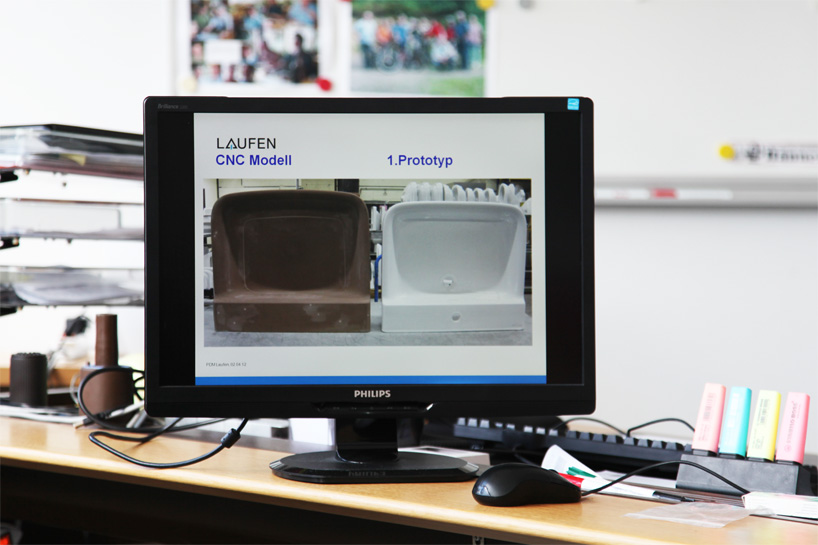
the design development team works with products from the first ideas stage, through design selection, mold-making, and prototype analysis and reworking
image © designboom
to maintain a forward-looking perspective, asking architects, interior designers, and retailers to identify current trends
in bathroom culture, and report on the needs and desires expressed by consumers. while the research doesn't exclude
physical attributes such as colour or silhouette, LAUFEN is increasingly finding the focus on what marketing and products
director marc viardot terms 'wellness 2.0', the seamless integration of functionality and aesthetic as they affect an individual's
experience, within the greater context of a home.
ultimately, however, a successful concept depends on successful execution, and in order for any proposed piece to continue on in
the LAUFEN design process, it must pass a rigorous 'visibility analysis' in a team meeting of the plant manager and supervisors
in the casting, glazing, and firing departments. here, these professional craftsmen examine a design to ensure that it can be
produced within the constraints that the ceramic material and production process defines.
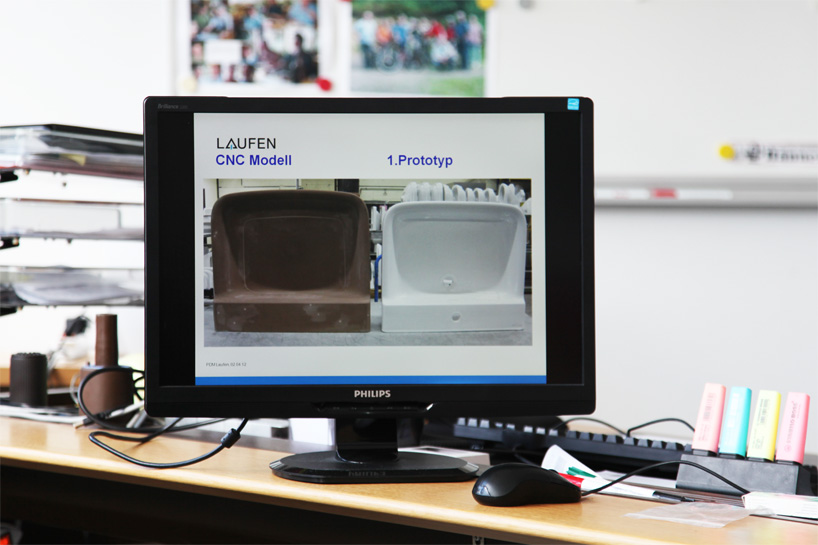
the design development team works with products from the first ideas stage, through design selection, mold-making, and prototype analysis and reworking
image © designboom
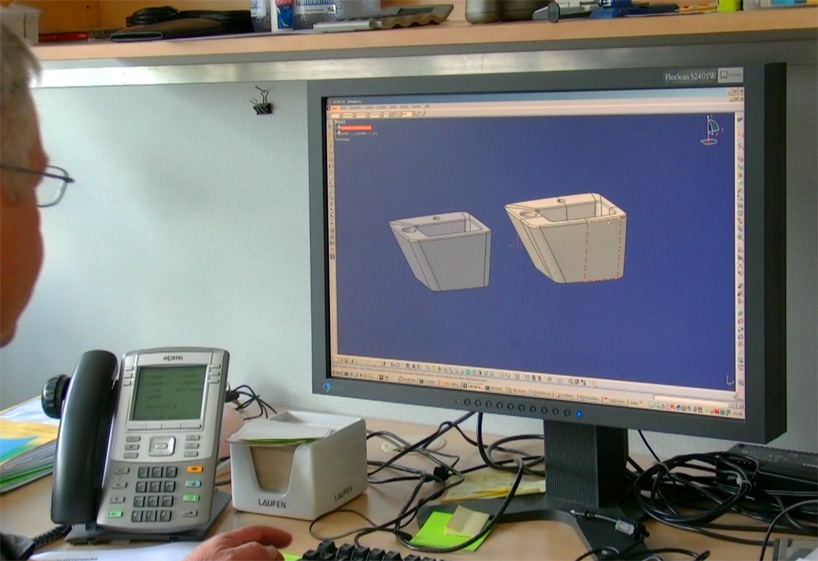
this design engineer is simultaneously viewing the dimensions of a piece pre- and post- firing in the kiln
image © designboom
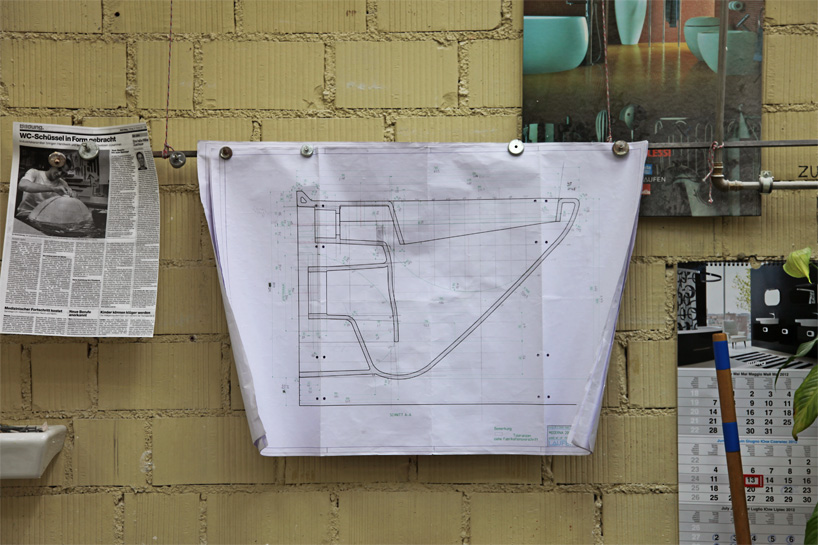
finalized designs become technical diagrams that workers use as they measure and optimize early run prototype models
image © designboom
once a particular design has been accepted as a good candidate for production, the piece must first be clearly outlined with a technical diagram,
in conjunction with quality assurance tables on all dimensions and acceptable tolerances in measurements. these will continue to be of importance
throughout the next several stages of prototyping, as the piece is reviewed and inspected at multiple points.
in the development offices of the LAUFEN factory, designers take on the first steps of prototyping, working with 3D modeling software
to draft new pieces, with an eye towards not only the exterior aesthetics but also the ways in which the interior will permit successful connection
with necessary piping. in particular, because different countries have different piping and drainage standards as well as different legal regulations,
every design must be adaptable to meet the codes of all countries in which it is planned to be sold. the designers note that practical testing of prototypes
after firing remains an extremely important part of the process, but they can already begin to efficiently design models for success by working first
in 3D sketching environments. this software is also particularly helpful to generate and compare the dimensions of models before and after firing
(whereupon they shrink).
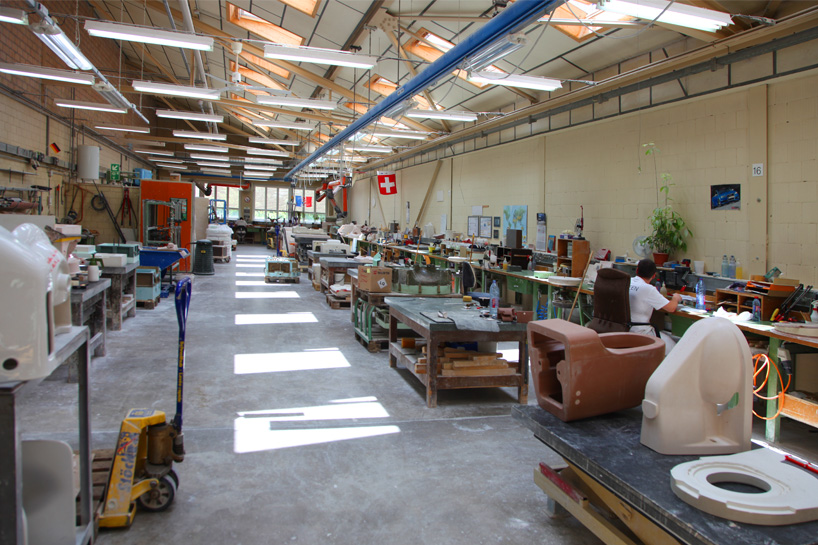
the design and development workroom
image © designboom
from the design and development offices, we head next to the model shop, a long, brightly skylit room whose evenly spaced worktables
are covered with models and ceramic casts. along the sides of the room, individual workstations include specialty tools, work notes, and the
occasional personal object, from soccer flags to living plants. it is here that the first 1:1 scale prototypes are produced. the first, one-off piece
of a design-- the 'CNC model'-- is produced by an external company and shipped to LAUFEN, where craftsmen first create a plaster "model mold",
from which they cast the first in-house prototype. molds vary in complexity from two pieces for most washbasins, to many internally fitted
small parts to create the holes and interior architecture of more complicated designs like toilets.
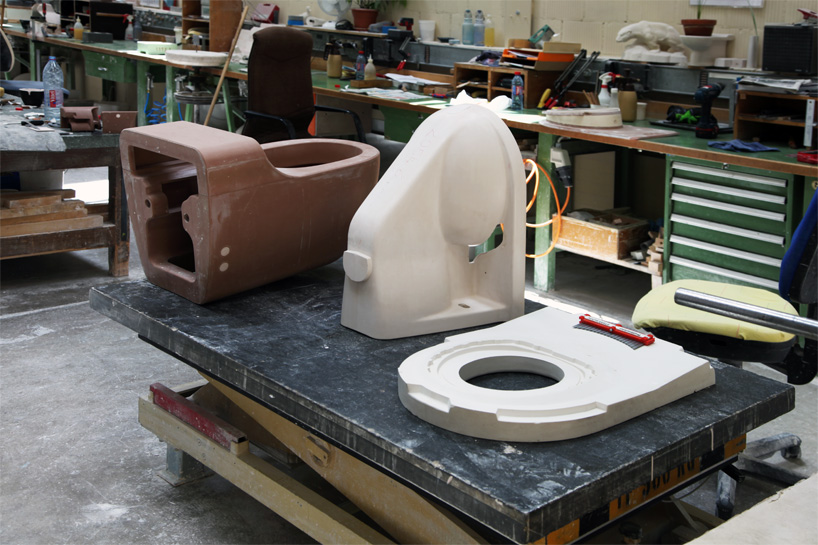
rubber mold and plaster cast
image © designboom
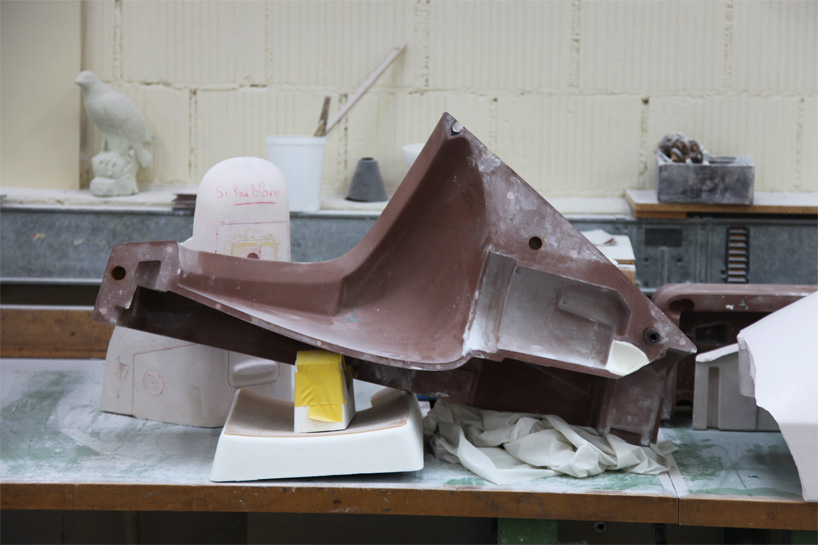
profile view of one piece of a mold, with engineering notes marked on the plaster cast visible behind it
image © designboom
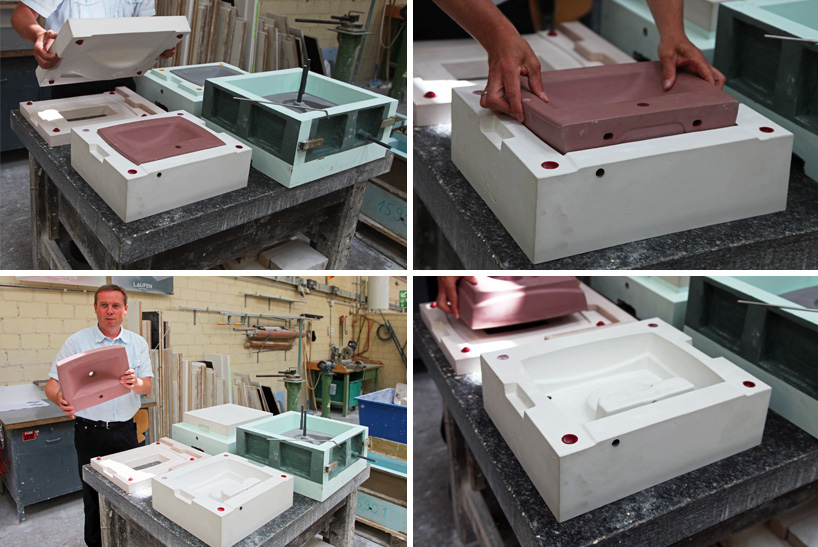
the first one-off edition of this small basin (reddish colour) is used by LAUFEN to generate the plaster 'model mold' whose use is demonstrated here
images © designboom
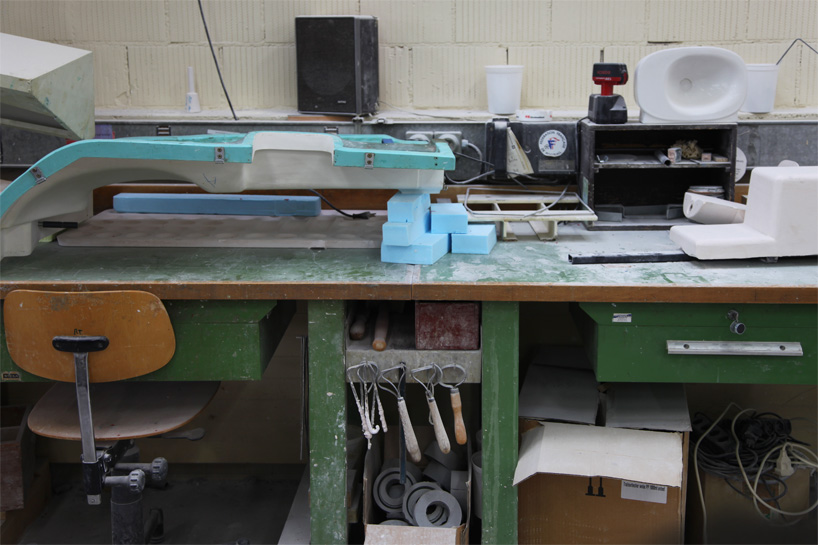
workstations along the edges of the room provide space for workers to carefully measure and work with early models
image © designboom
in this space, craftsmen are also working with prototype casts to notate by hand any necessary corrections for deformation caused
by shrinkage during firing. this is just one of several ways in which it is evident that review and optimization remain a part of the design
process from the first inkling of a new concept through to the shipment of completed pieces; ceramic is a natural material, and so designers
must think carefully about the properties and limits of the material as they conceptualize their works. although LAUFEN's precise methods
of testing the ceramic slip material ensure that all production line pieces are being formed from uniform, high-quality ceramic, the process
of molding the first few prototypes of a new line can sometimes highlight unexpected behaviour of the material as it interacts with the shapes
and points of tension of the designed form.
as a result, the first prototypes of a series are produced on the LAUFEN factory floor, but are each examined in the model shop,
where measurement corrections are marked by hand on the piece. from these calculations, the model mold is then altered.
through this process, often up to three to five prototypes are created before the results meet LAUFEN's strict technical standards
and tolerance restrictions.
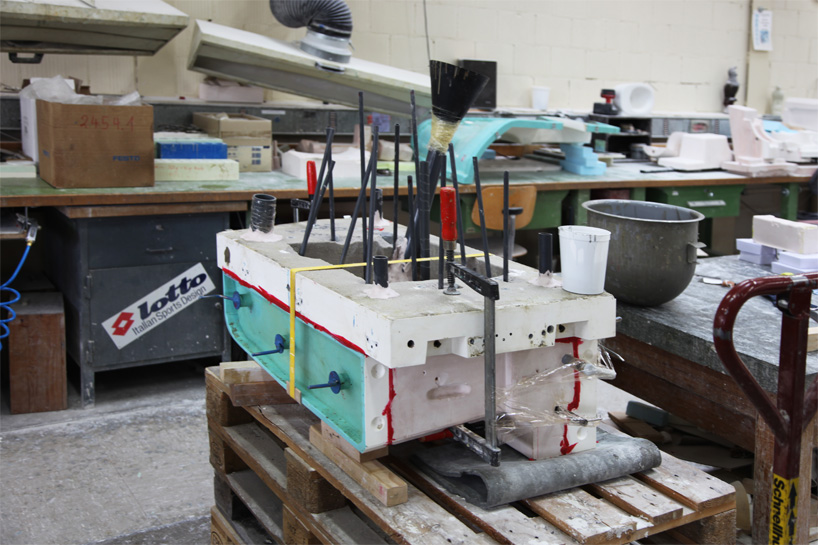
image © designboom
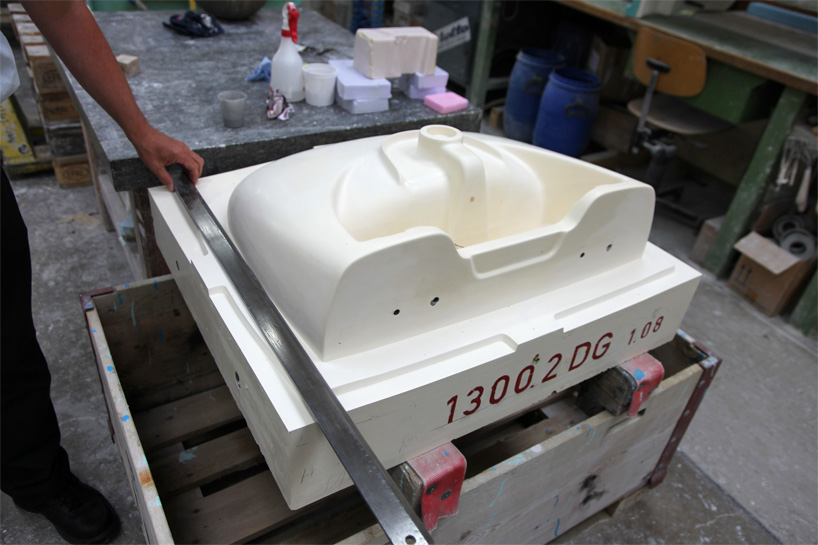
craftsmen must measure carefully to make sure that prototype casts represent the precise dimensions and forms specified in their technical sheets, and did not suffer deformation during firing
image © designboom
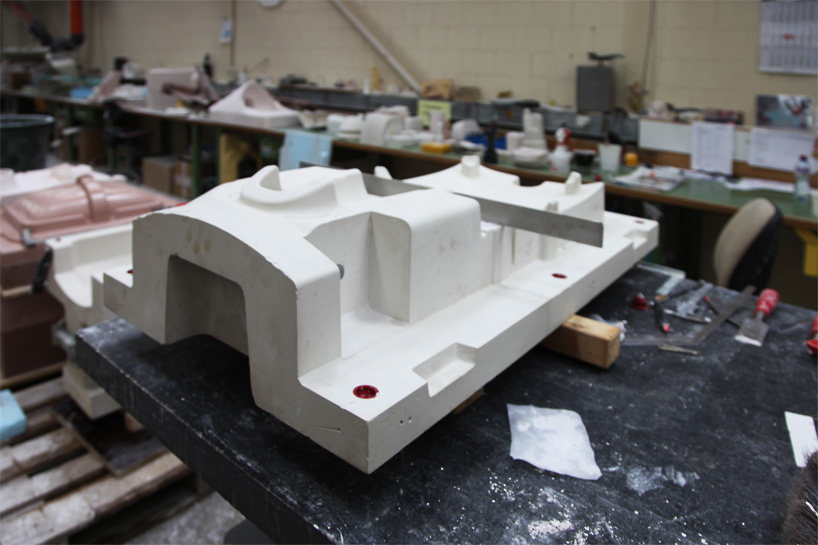
additional view of workspace as a piece is being measured and carefully modified with the hand tools seen on the table to meet design specifications
image © designboom
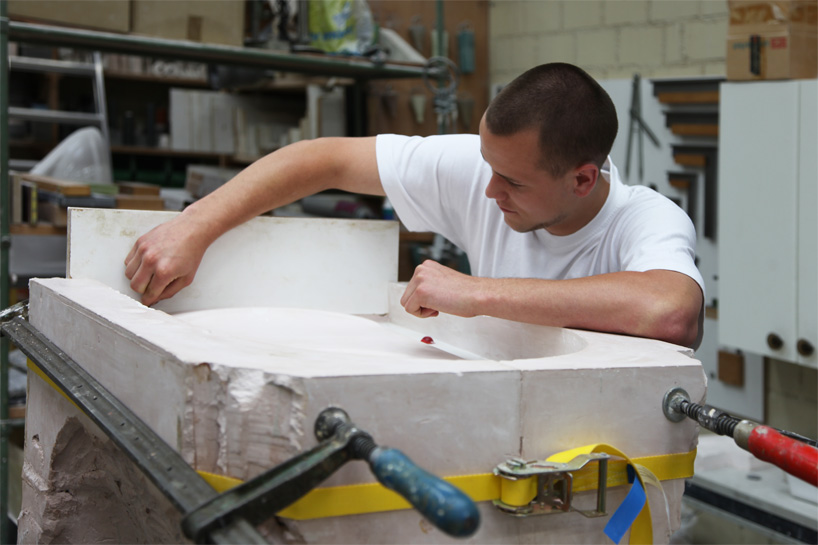
closer view as jannik stöckli, an industrial ceramics apprentice, sands down a cast to meet technical specifications
image © designboom
once the prototype casts are coming out properly, LAUFEN creates the case mold, composed of plastic and rubber (enabling the release of ceramic
casts once they have dried), and then the pressure-casting mold if one is being used in this product line. finally the first pilot series can be produced,
also through regular methods on the production floor. at least 20 pieces are formed, glazed, and fired, before undergoing close inspection to ensure
that the casting techniques have successfully translated to higher quantities.
if it has, each future piece is still subject to the strict quality controls that LAUFEN puts on every object produced in its factory, but the line has
successfully entered the production phase.
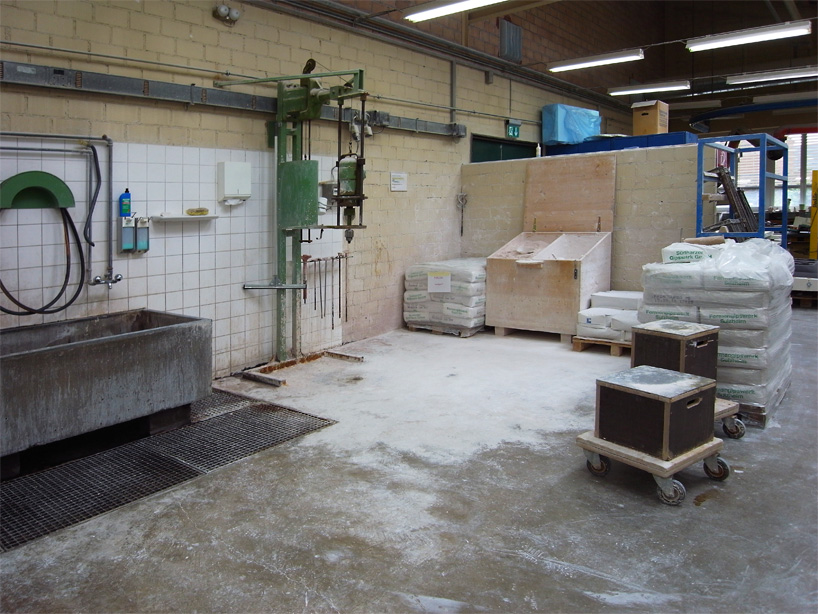
raw materials used in the creation of ceramic are also housed in the development and prototyping workspace
image © designboom
alberto magrans, senior managing director, on the challenges of working with ceramic and the innovative potentials of the material that the company is currently pursuing
19/10/12
Guitarras.
Algo mas de esto...
guitarra,
maderas,
Materiales,
proceso creativo
18/10/12
Una gran idea, como resolver un problema.
Vía: http://www.kickstarter.com/projects/baker/airtracks-inflatable-all-terrain-camera-slider
Algo mas de esto...
ideas,
Kick starter
Sillita.
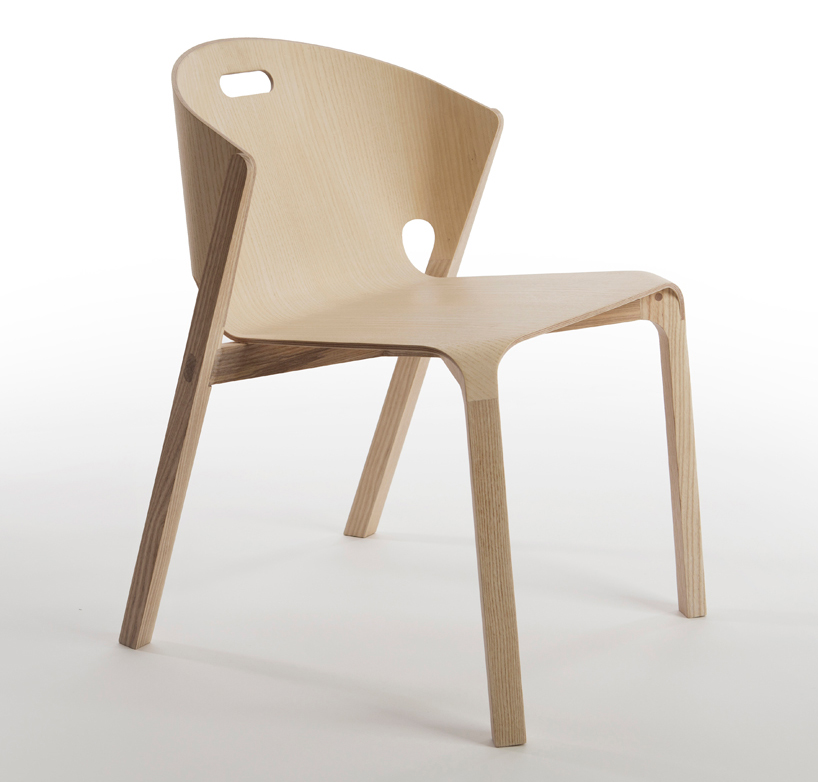
'pelt' chair by benjamin hubert for de la espadaH740mmx W460mm x D540mm
'pelt' is a chair made from a thin 8mm plywood shell that wraps around a solid ash frame. conceived by benjamin hubert
for furniture brand de la espada, the seating design extends downwards through the front legs making it appear as a seamless unit,
integrated with the solid frame beneath. the front and rear legs of the chair are linked via a simple cross construction which
offers overall stability and support.
for furniture brand de la espada, the seating design extends downwards through the front legs making it appear as a seamless unit,
integrated with the solid frame beneath. the front and rear legs of the chair are linked via a simple cross construction which
offers overall stability and support.
this geometric arrangement is a result of CNCing a complex twist to maintain the integration; of the start and end points.
the chair offers efficient stacking with its ability to put six together. the collection was developed over a period of 12 months
after several iterations of prototyping and testing.
the chair offers efficient stacking with its ability to put six together. the collection was developed over a period of 12 months
after several iterations of prototyping and testing.
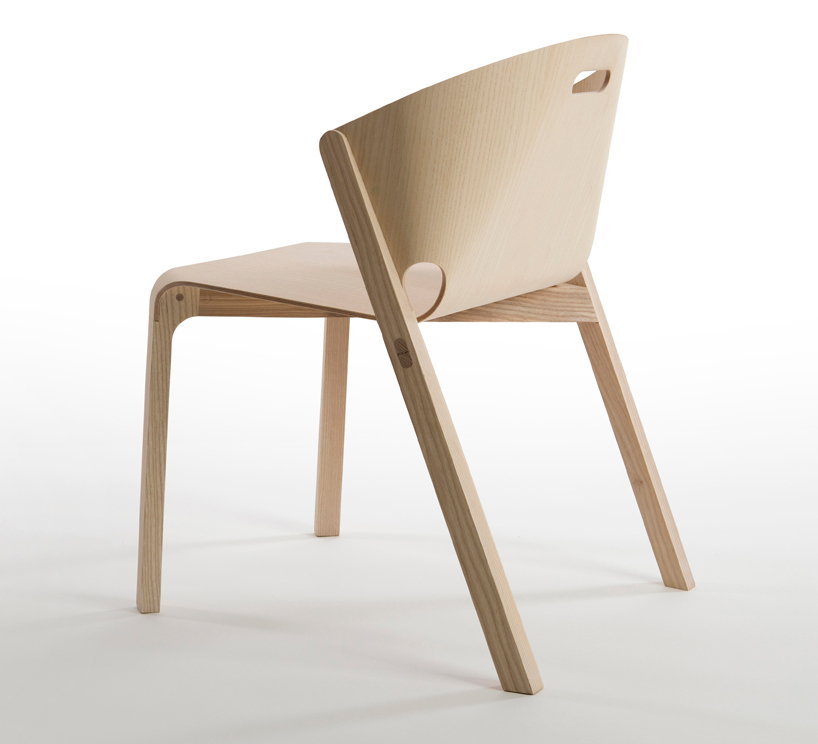
3/4 back view
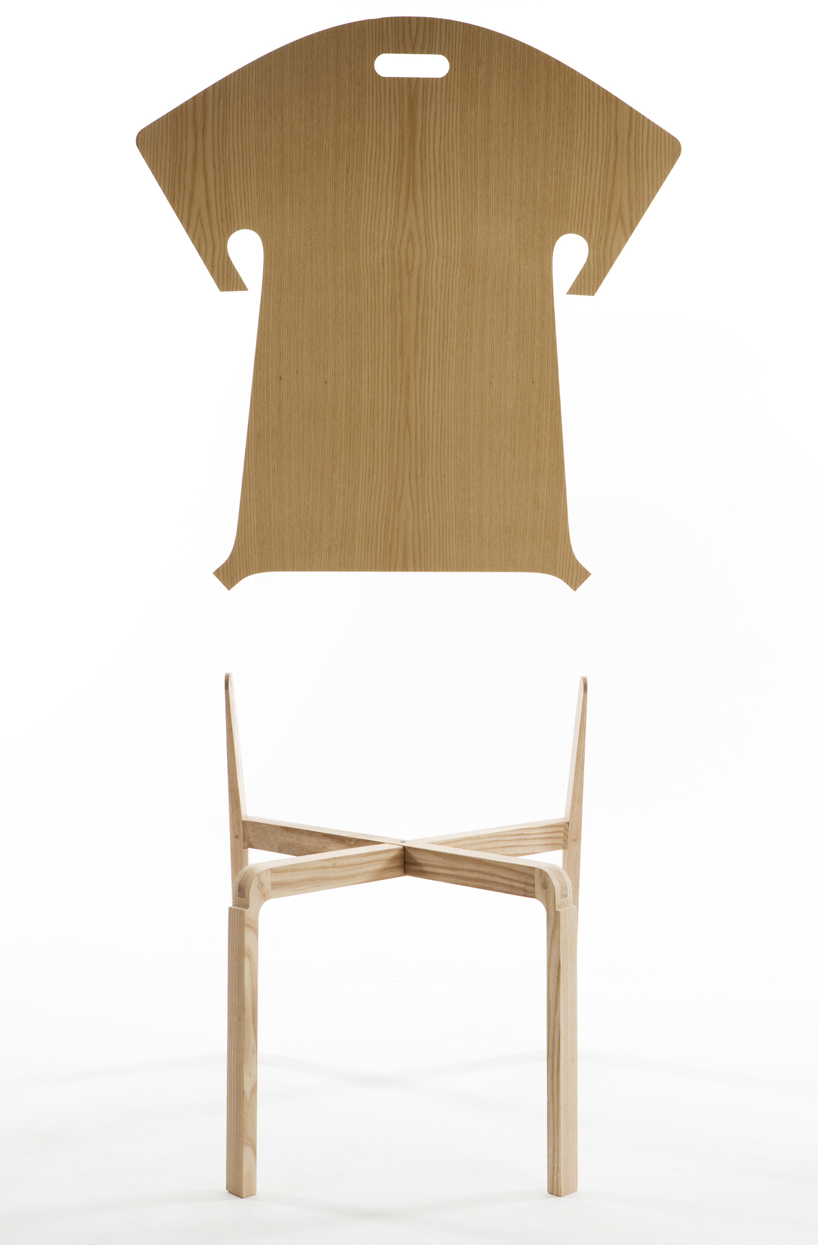
components which make-up 'pelt'
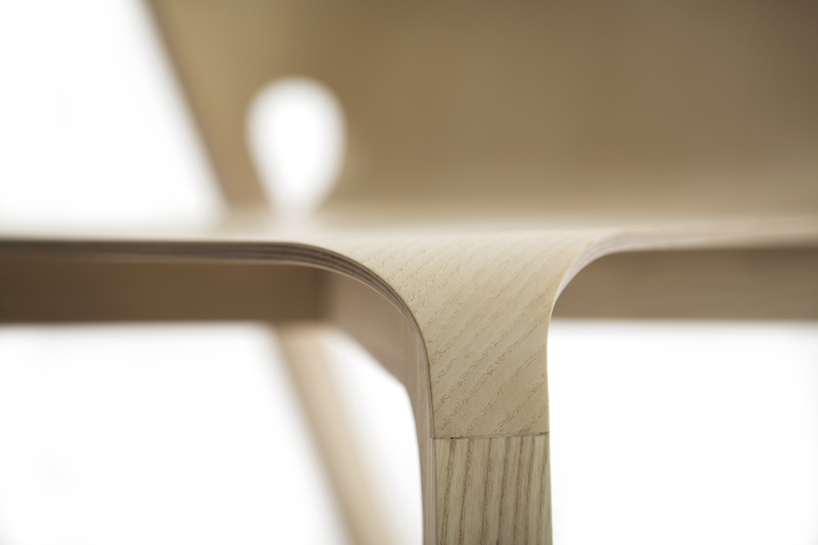
front leg detail
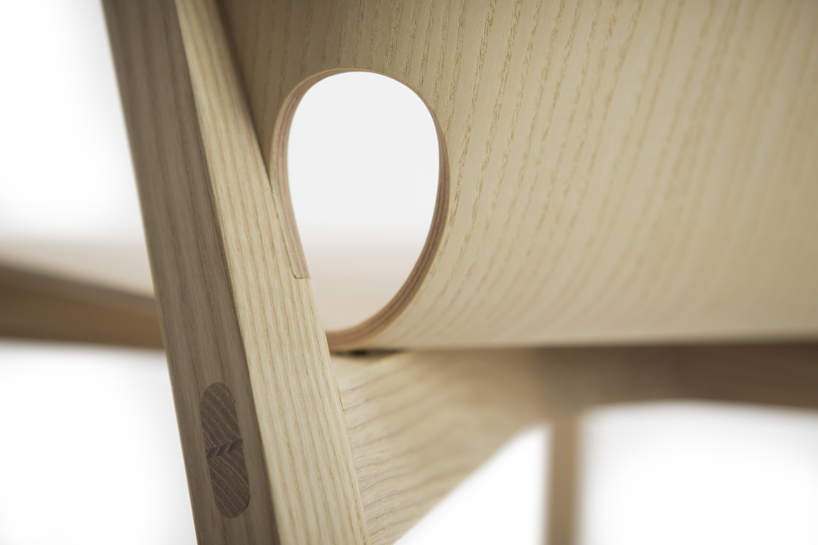
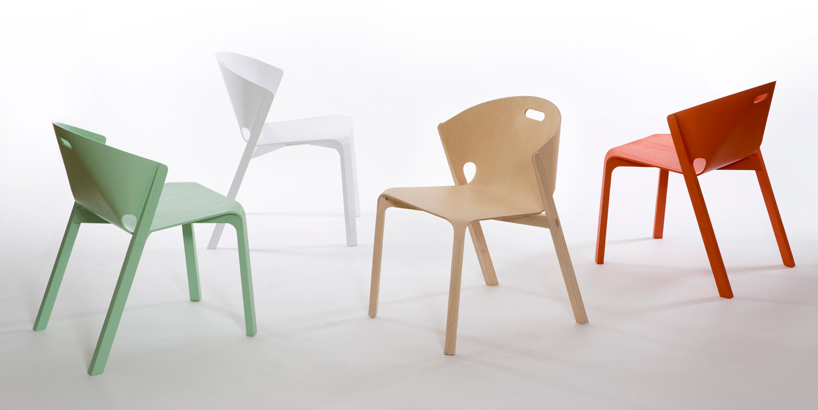
color variations
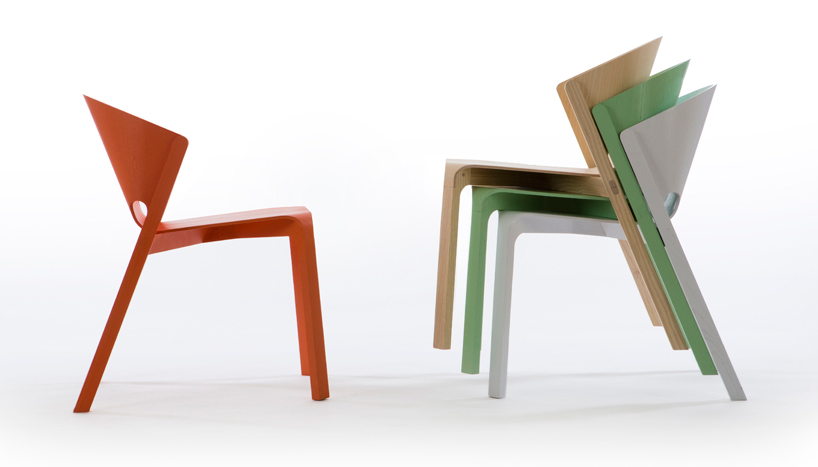
'pelt' can be stacked up to six at a time
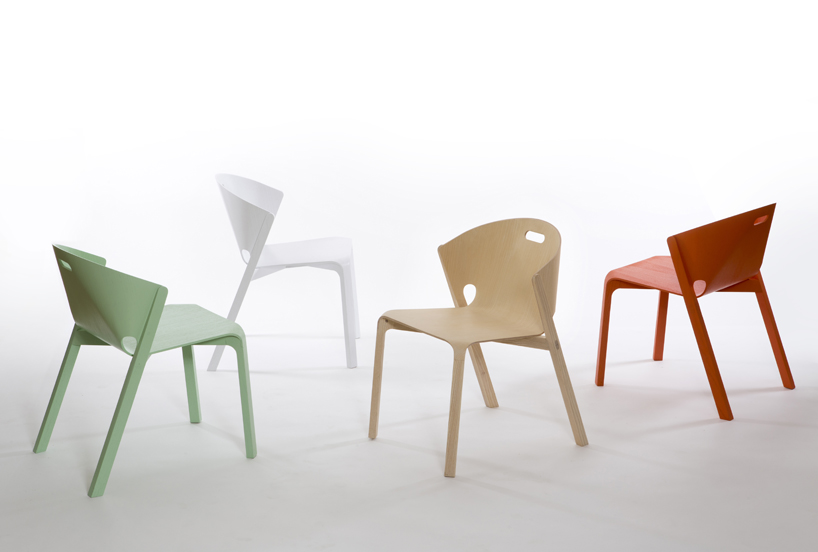
pelt group
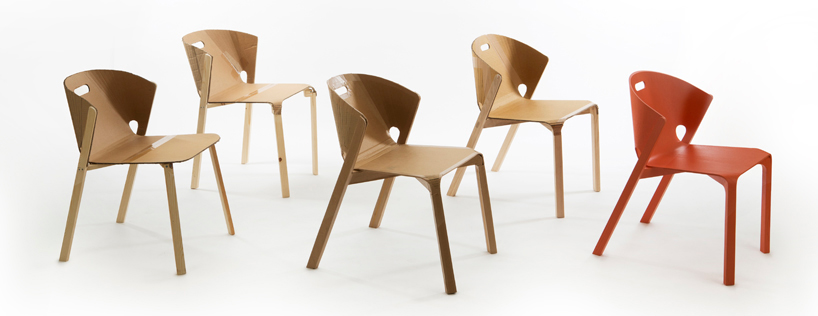
prototype development
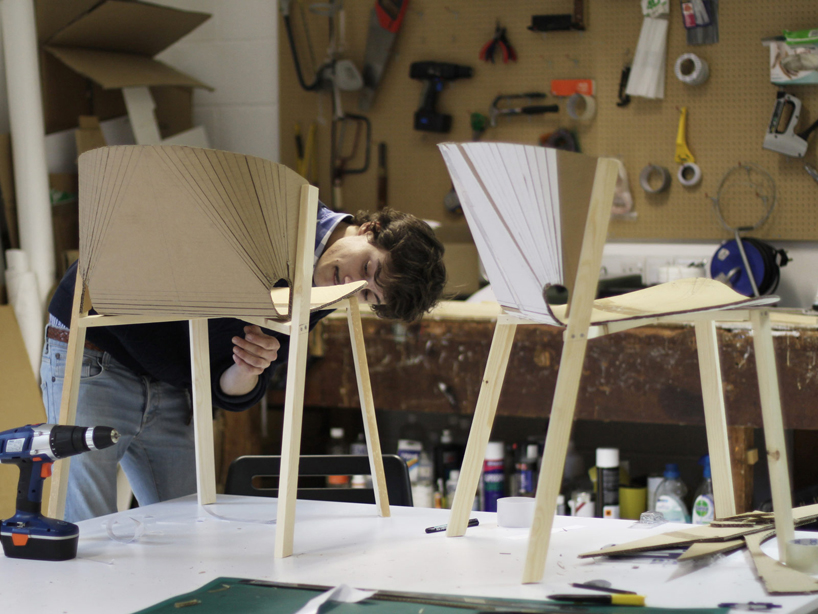
developing the prototype models of the chair out of wood and cardboard
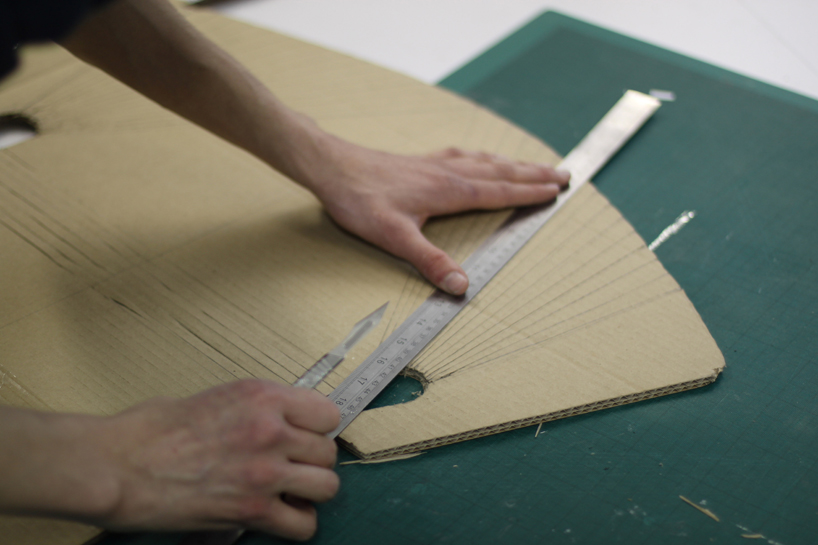
cardboard prototypes
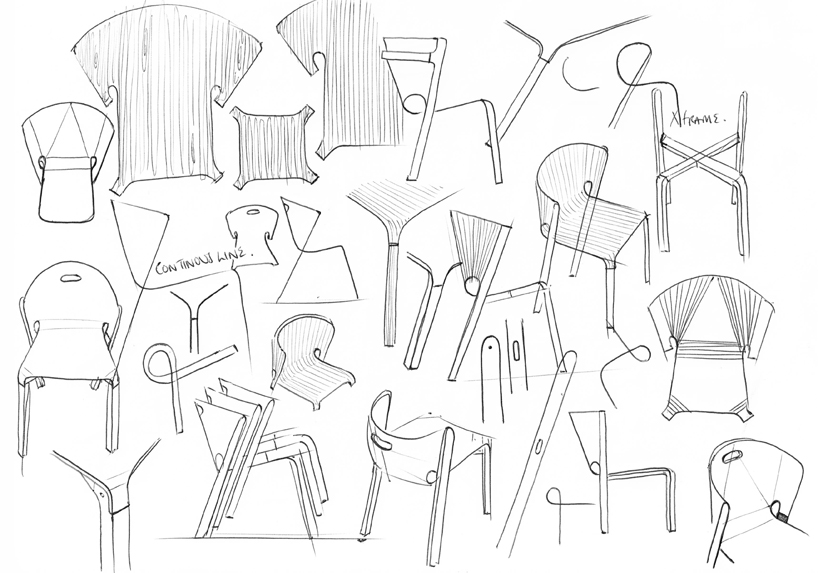
concept sketches
designboom has received this project from our 'DIY submissions' feature, where we welcome our readers to submit their own work for publication.
see more project submissions from our readers here.
Algo mas de esto...
madera.,
proceso creativo,
Sillas
Bien diseñadita-
VELA cycle trainer by LUNAR from LUNAR on Vimeo.
vía: https://vimeo.com/40264396#
Algo mas de esto...
bicicletas,
diseño
Un poco de "Arte"
Santos Bregaña-
Algo mas de esto...
arcilla,
arte,
Diseñadores
Hacer puente.- Fácil, lindo y barato. Mentira un quilombo.
Puente de bamboo.
Vía: http://www.designboom.com/weblog/cat/9/view/24123/pt-bamboo-pure-millenium-bridge.html
Vía: http://www.designboom.com/weblog/cat/9/view/24123/pt-bamboo-pure-millenium-bridge.html
Algo mas de esto...
Bamboo,
estructuras.
Bamboo.

'gang rou' chair by jeff dayu shi
jeff dayu shi, founder and creative director of dragonfly gallery and dragonfly design center, is a taiwanese designer who through
his practice employs the use of bamboo in the construction of his furniture and interior projects. during beijing design week 2012,
he presented 'praise of bamboo far and near' an installation of selected bamboo works which included chairs and tables.

the chair's profile which shows the fan effect of the four curved bamboo slats which make up the back rest
drawing influences from the furniture forms of the ming and qing dynasty, shi's 'gang rou' armchair features a round-back
with a simple linear structure. the stackable seating piece appears heavy because of its large size, but its bamboo construction offers
a lightweight design which is easy to carry. its S-type backrest curves to the human spine.

front view of the chair which draws its formal qualities from the furniture of the ming and qing dynasties
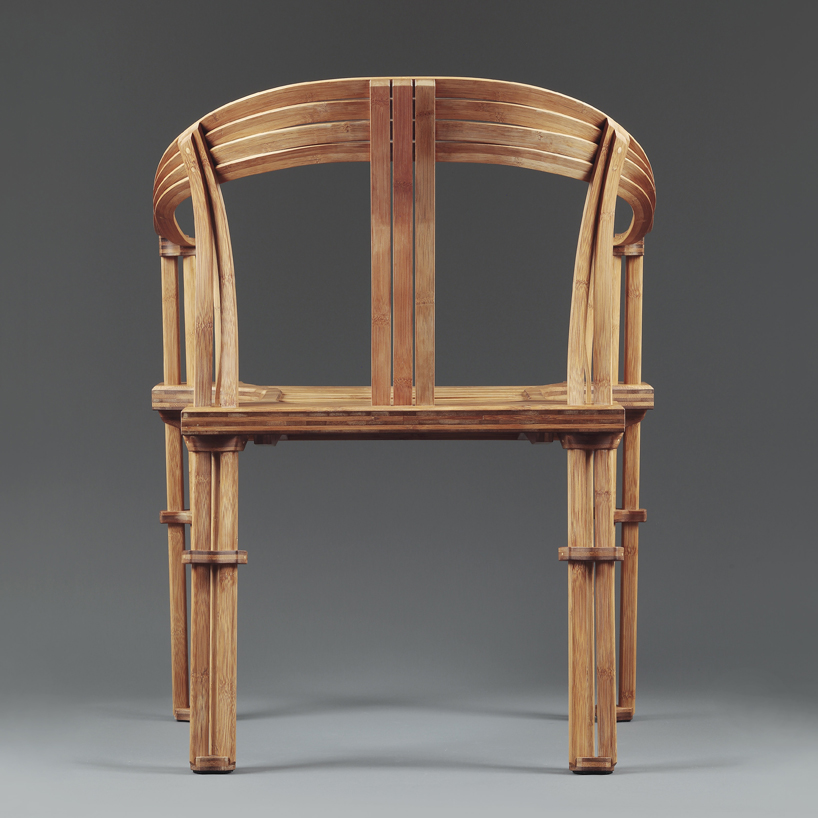
bentwood slats of bamboo form the 'S' shaped backrest

top view of the seat

the bamboo chair is stackable
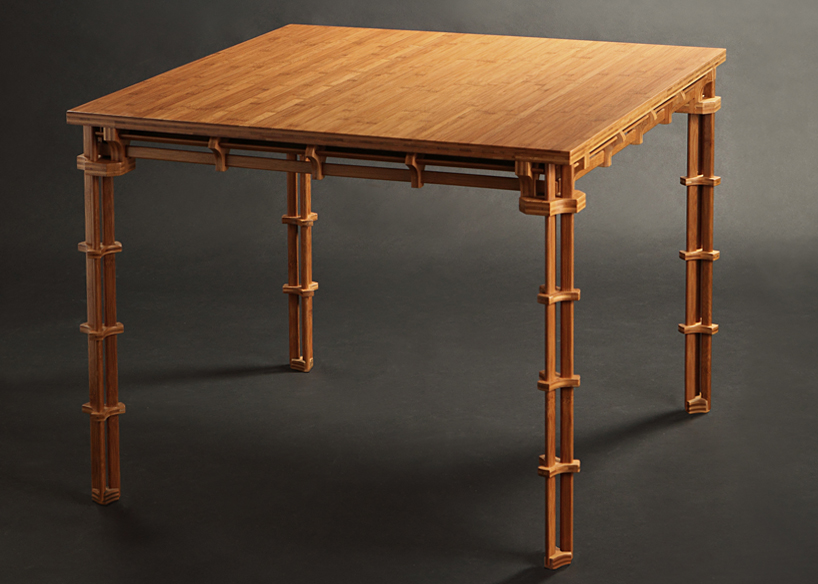
'zhuo ba xian' table
in chinese families, the 'ba xian table' is traditionally one of the most common pieces of furniture within the household.
composed of only three parts: the top, the legs and the aprons, historically they have been made from various types of hardwood -
many of which are on the verge of extinction today. shi's 'zhuo ba xian' bamboo version employs a mortise and tenon joint system,
and use of a sustainable material resulting in a more contemporary expression of the classic table.
the legs are composed of three bamboo slats which intersect with one another at an angle of 120 degrees.
a diaphragm-like mechanism holds these parts together, giving structural strength and high rigidity to the design.
'zhuo ba xian' is produced in collaboration with craftsmen: huang chun-chieh (ruban craft academy)
and wang deng-fa (yung shing furniture co., ltd.).

the table is constructed employing a mortise and tenon joint system
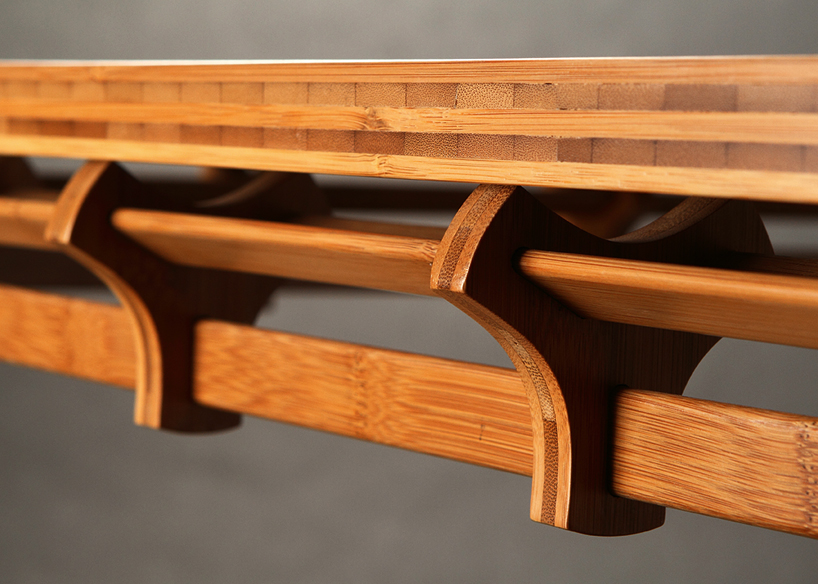
detail
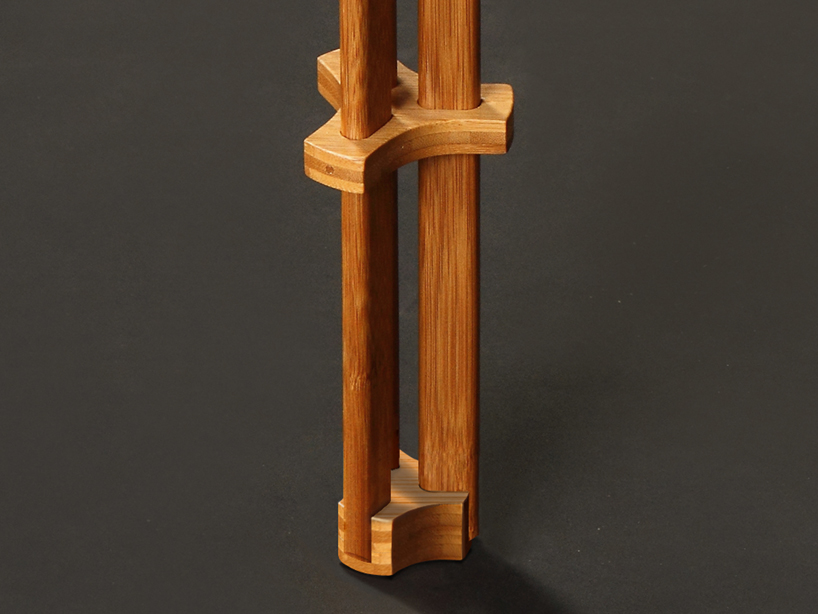
the legs of the table are made-up of three slats which intersect one another at a 120 degree angle and are held in place by a diaphragm-lie component
vía: http://www.designboom.com/weblog/cat/8/view/24116/beijing-design-week-bamboo-furniture-by-jeff-dayu-shi.html
Suscribirse a:
Entradas (Atom)